SPRAY FOAM INSULATION GUIDE FOR HOMES AND BUILDINGS
BUILD IT TIGHT, VENTILATE RIGHT.
SPRAY FOAM IN THE BUILDING ENVELOPE
The building envelope is a total system of construction materials and design components that control the temperature, movement of air, and moisture both into and out of the building. A building's insulation, air barrier and vapor barrier all need to work together to achieve a more stable, comfortable and healthier indoor environment. Many new materials and design practices are being implemented to extend the sustainable service life of buildings and homes.
Challenging the Notion of Passive Ventilation
Building Tight, Healthy, and Energy Efficient Homes
Ventilating the attic and crawl spaces has long been the traditional and code-required method of home design and building. However, ventilation of these spaces was required because standard materials and building design practices were not capable of addressing radiant heat transfer, condensation, and the results of “stack-effect issues.”
In order to address heat transfer from weather issues, utilities, and the formation of moisture due to condensation and air infiltration, the only option was to ventilate the attics and crawl spaces. The major problem with ventilating these spaces is that the air brings moisture, pollution, and other adverse problems and challenges with it. Furthermore, the vents to allow it in create voids in the building for insects and rodents to enter, and all our nice, conditioned air that escapes or is pulled from the living spaces to exit.
In fact, in the summer, the incoming air needs power-consuming fans to bring it in, and it will never get any cooler than the outside air temperature. Why would we want 95-degree-hot, humid, potentially pollution-ridden air into our attic and crawl space? In the winter, this air is freezing cold.
If our heating and cooling utilities and ducts are located in the attic and/or crawl spaces (most usually are), then their radiant contact with the ducts will cause them to lose up to 10% or more of the hot or cold air flowing through them due to radiant transfer. Worse yet, moisture and mold can also form within the ducts during certain temperature conditions, causing adverse health effects for the building occupants or your family.
Structural Integrity, Energy Efficiency, and Air Quality
Enhancing Home Performance
Another major reason that traditional methods call for attic ventilation is that during the hot summer months, heat from the sun builds on the roof and radiates into the attic space. In fact, it can build to upwards of 130 to 150 degrees or more. (See our section on Urban Heat Islands.) This extreme heat radiates into the attic and the living space, causing condensation and the potential for mold. Our air conditioning systems also need to work harder and consume more energy with all this heat directly above our heads. The extreme heat also makes it very uncomfortable to enter these spaces.
Most builders and design professionals are not familiar with modern materials and progressive building science techniques that can virtually eliminate all of these problems that force the traditional, less effective requirement for ventilation in these building spaces. Builders and design professionals will also make the argument that your home needs to breathe. Well, they are absolutely correct. But why rely on cracks, gaps, and holes in your building for passive ventilation when you can build your home tight, healthy, and energy efficient and let the mechanical ventilation systems do the job properly?
Spray foam insulation can still provide benefits far greater than traditional materials such as fiberglass and cellulose, regardless of whether you decide to ventilate these spaces or not. By using spray polyurethane foam insulation, you can increase your home's energy performance, structural integrity, and air quality.
POLYURETHANE FOAM STRENGTHENS YOUR HOME
The walls in your home are the main structural component of the building. In wood frame construction, the weight of the roof, shingles, standing rainwater, and any snow adds weight and exerts downward forces on the walls, resulting in a compressive force.
The walls in your home are the main structural component of the building. In wood frame construction, the weight of the roof, shingles, standing rainwater, and any snow adds weight and exerts downward forces on the walls, resulting in a compressive force.
Strong winds and gusts from storms also impose lateral forces on your home’s walls. These forces can distort the walls with what is called a “shearing force.”
Building codes require that your home’s walls be designed to withstand these various forces and loads. However, when walls are built to just the minimum standards while still being safe, symptoms of movement such as creaking and shaking during high winds or occupant usage often occur.
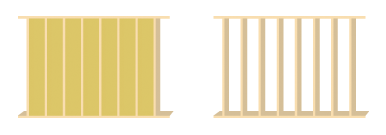
Stud wall as built Stud wall under shear load (exaggerated)
Higher-density, closed-cell spray foam insulation inside your stud walls fully adheres to both the exterior sheathing and the studs, reinforcing both. With this added rigidity, there will be less wall movement due to wind, vibration, and occupant activity. Additionally, your walls have greater than code-required resistance to "racking events" such as hurricanes or other strong wind situations.
SPF can also add structural strength to buildings. NAHB Research demonstrated SPF-filled walls could add from 75% to 200% racking strength to walls of OSB, plywood, light gauge metal, vinyl siding, or gypsum board.
Racking Test
Shearing forces on a wall tend to distort the wall from its original shape as a rectangle into a parallelogram. To test a wall’s resistance to the shear forces imposed by wind loading, engineers use a "racking test." An 8 ft. x 8 ft. model wall is built and placed in a large frame. The base of the wall is secured to the frame, and a horizontal (lateral) force is applied at one upper corner. The force is increased by 400 lb. increments until the wall structure fails.
Spray foam’s effect on wall strength
In a series of racking tests, walls with and without spray-applied polyurethane foam insulation were compared. Two exterior-facing materials were tested:
- Vinyl siding over 15 lb. building paper; and
- Textured plywood siding.
All wall panels were faced with ½-inch sheetrock on the interior side and used 16-inch stud spacing. For the stud wall panels that were insulated with spray-applied polyurethane foam, the stud cavities were essentially completely filled with foam of 1.5 lb/ft³ density.
As the graph indicates, stud walls filled with spray-applied polyurethane foam add significant strength to home walls. Furthermore, for each load applied, the foam-filled walls deformed less and offered greater resilience.
In a second series of racking tests, spray-applied polyurethane foam insulation was compared with conventional R-19 glass fiber batts. In one comparison, the wall panels were faced on both sides with dry wall. In the other comparison, the wall panels were faced on one side with OSB (oriented strand board) with dry wall on the opposite side. In both cases, the wall panels used steel studs spaced 24 inches apart, and the average foam density was 2.26 lb/ft3.
Once again, the graph indicates the greater strength of the spray foam-insulated wall system.
In a second series of racking tests, spray-applied polyurethane foam insulation was compared with conventional R-19 glass fiber batts. In one comparison, the wall panels were faced on both sides with dry wall. In the other comparison, the wall panels were faced on one side with OSB (oriented strand board) with dry wall on the opposite side. In both cases, the wall panels used steel studs spaced 24 inches apart, and the average foam density was 2.26 lb/ft3.
Once again, the graph indicates the greater strength of the spray foam-insulated wall system.
Test 1: Test results are reported in "Testing and Adoption of Spray Polyurethane Foam for Wood Frame Building Construction" (May 25, 1992), prepared by the NAHB Research Center for the Society of the Plastics Industry/Polyurethane Foam Contractors Division.
Test 2: Test results are reported in a letter from Bob Dewey, Mechanical Engineer, NAHB Research Center, to Mason Knowles, The Society of the Plastics Industry/Spray Polyurethane Foam Division (November 18, 1996).